PROTOTYPING
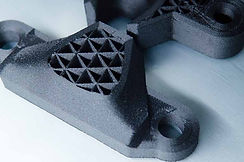
3D PRINTED PROTOTYPES
Stärke Tooling has multiple 3D printers onsite which are used to assist in customer product development but also are available as a bureau service.

PRESS METAL PROTOTYPES
Stärke Tooling can provide a range of techniques best suited to product shape, complexity and volume required in determining a prototyping strategy for press metal parts.
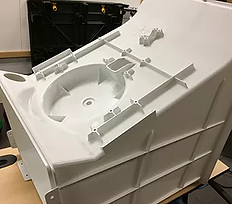
MACHINED PROTOTYPES
Quite often to achieve large size, dimensionally accurate prototypes greater than 750mm ( 30 inches ), Computer Numerical Control, (CNC) machining is required. This is an area in which we excel with over 35 years of complex 3D machining experience behind us coupled to a fleet of precision 5 and 7 axis machine tools.
Machining is also useful and economical in producing certain types of products that will eventually be cast.
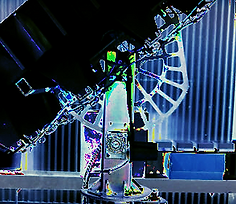
FABRICATION PROTOTYPES
Stärke Tooling has considerable expertise in the use of laser, waterjet and plasma cutting coupled to precision fabrication equipment .
If you require components and assemblies fast then Stärke Tooling can lend a helping hand.

CASTING PROTOTYPES
3D printed patterns, core boxes and
plaster moulds for high and low pressure aluminium.
Gravity / sand cast low volume solutions as well as fully machined parts where appropriate to gauge components and validate fitments.
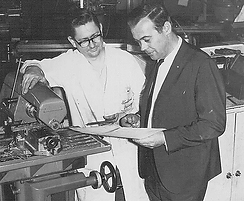
INNOVATION IN PROTOTYPES
The genesis for the Starke-AMG Alliance, was the founder of Precise Plastic Tooling, the late Manfred Tinney in 1971.
Manfred's engineering career started straight from school as an apprentice at BMW in their Spandau factory in Berlin. He later worked as a Tradesman, manufacturing tooling and jigs for both the BMW 801 high performance piston engine as well as the BMW 003 Axial Flow Jet Engine, which together with the JUMO 004 engine, ushered in the Jet Age. After arriving in Australia in 1951, Manfred worked in various toolmaking roles, mainly in the cavity tooling area prior to commencing his own business.